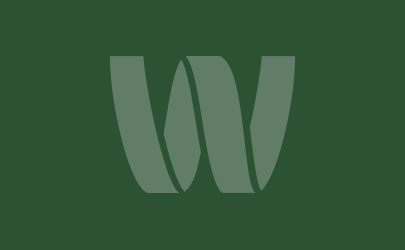
Successful Pipeline Cleanouts Using Jointed Pipe
Share:
Challenge
Paraffin and asphaltene deposition, along with hydrate formation, can often lead to expensive and time-consuming efforts in attempts to cleanout pipelines and restore flow assurance. Multiple cleanout runs and remediation efforts are often needed to adequately cleanout the pipeline, costing the operator millions of dollars through the cost of equipment, rig time, and loss of production.
Coiled tubing is often the first deployment for cleaning out pipelines due to the initial associated cost, ease of rigging up the coiled tubing unit, and the less complicated setup compared to a snubbing unit/hydraulic workover unit (HWO). Though coiled tubing is slimmer, smaller, and more flexible than jointed pipe, it also has limitations that can prevent a successful cleanout run including the limited circulation ability due to the smaller ID, lack of stiffness leading to buckling, and difficulty in rotation, all of which can affect the ability of the coiled tubing in achieving a successful cleanout and reaching the total depths required.
Solution
Over the past 15 years, Workstrings International has designed and modeled numerous successful pipeline cleanout strings for operators and snubbing/HWO service companies looking to use jointed pipe to cleanout their pipelines. By using jointed pipe in conjunction with a snubbing unit, many of the limitations of coiled tubing can be avoided and the cleanout can become a more cost-efficient operation due to the speed and efficiency in reaching the desired cleanout depths which are 4-5 miles laterally with the ability to snub, push, and rotate the pipe.
Working in consultation with the operator and snubbing/HWO service workover teams to ensure operational demands are met while allowing for the greatest safety factor, Workstrings Engineering cleanout string designs have been used to cleanout pipelines with actual depths reaching as far as 28,789 ft. and with pipeline internal diameters as small as 4.0 in. For several of the pipeline cleanout designs, calibration work was done by Workstrings to improve accuracy of the modeling, allowing for a greater degree of certainty when modeling the pipeline cleanout string, and determining optimal operational parameters. This calibration modeling has supported operators during real time operations.
Common challenges when designing pipeline cleanout strings using jointed pipe include diameter limitations of the pipeline, trajectory of the pipeline, torque capacity issues if reaming through hydrate and paraffin accumulation is necessary, riser to pipeline transition, and limiting the degree of buckling as much as possible. These pipeline cleanout operations have been successfully performed from both platform facilities and intervention vessels.
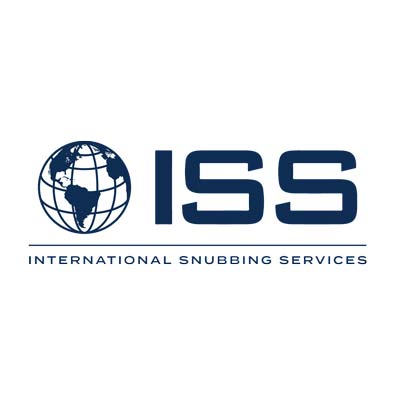
“Use of HWO Units and jointed pipe have saved operators millions of dollars in service costs and getting production back online as quickly as possible”
John Hardy
VP of Operations, International Snubbing Services
Results
Across all pipeline cleanout string designs provided by Workstrings Engineering, each design has proved successful with positive feedback being generated by the operator and snubbing/HWO service company, with the most recent pipeline cleanout string designed by Workstrings Engineering being used to set a new offshore snubbing/HWO world record for the longest subsea pipeline cleanout by reaching 28,789 ft. actual depth, using a 2-7/8” CTM26 and 2-7/8” PH6 tapered cleanout string and conducted onboard the Helix Q4000 Intervention Vessel. The highlight of this operation was to successfully clean out the flowline from the Q4000 rather than cutting the flowline up into sections which has been performed previously on long flowlines such as this one. This significantly reduces the number of critical subsea lifts, the HES exposure and overall timeline for the flowline abandonment. The flowline was lowered subsea with the deployment rigging and drill string where it was laid back in the original trench on the sea floor. This is another benefit of being able to perform the full cleanout in a single lift and requires the least amount of onshore disposal of flowline components.
Common Workstrings International pipe used for pipeline cleanout operations is shown below in Table 1, with tapered strings often being used to provide the optimal design.
Workstrings International Pipe Used for Pipeline Cleanout Operations
OD (in) | Connection | Grade | Wall (in) | Nominal Weight (lb/ft) | Max MUT (ft-lbs) | Premium Tube Tensile (lbs) |
---|---|---|---|---|---|---|
2-3/8 | PH-6 | P-110 | 0.254 | 5.95 | 3,400 | 145,371 |
2-7/8 | PH-6 | P-110 | 0.276 | 7.90 | 4,400 | 194,099 |
2-7/8 | CTM26 | V-150 | 0.362 | 10.40 | 10,100 | 333,070 |
2-7/8 | XT27 | S-135 | 0.362 | 10.40 | 7,100 | 299,763 |
3-1/2 | NC38 | S-135 | 0.368 | 13.30 | 12,100 | 381,870 |
4 | XT39 | S-135 | 0.330 | 14.00 | 21,200 | 403,526 |
5 | NC50 | S-135 | 0.362 | 19.50 | 30,700 | 560,763 |
Table 1 - Workstrings International Pipe Used for Various Pipeline Cleanout Operations
Date of Design | Vessel | HWO Unit | Type of Cleanout | TD (Designed or Actual) | ID of Pipeline |
13 April 2020 | Helix Q4000 | SBS Energy | Pipeline Decommission | 29,000’ Planned 28,789’ Actual | 4.775” |
14 May 2019 | Spar | ISS | Spar Column/Pipeline | 29,283’ Planned | 5.125” |
27 May 2015 | Spar | ITS | Pipeline | 21,000’ Planned | 5.410” |
08 April 2014 | Spar | Spar Column/Pipeline | 18,077’ | 4.000” | |
06 Sept 2011 | Spar | ISS | Pipeline | 20,555’ | 5.625” |
04 June 2010 | Spar | Export Pipeline | 21,806’ | 16.000” | |
28 Sept 2005 | Helix Q4000 | Pipeline | 25,000’ Planned 23,800’ Actual | 6.893” |
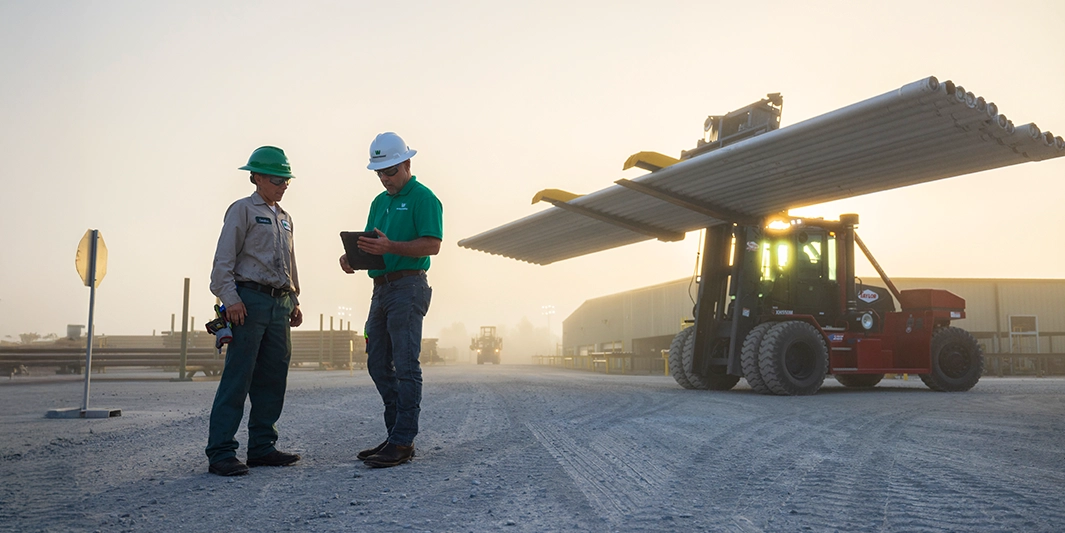
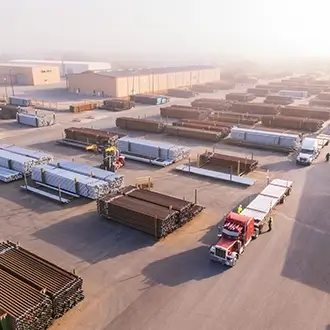
Let’s Tackle Your Biggest Challenges
From rental tubulars to custom-engineered solutions, Workstrings redefines limitations to help you secure success in your land, offshore, or deepwater projects. Let’s discuss your needs.